Questions & Answers
FAQ – S-Rating
Where can I find the information on the S-Rating of my company site?
You can find the information on the S-Rating of your specific location by logging onto the ONE.KBP ( www.vwgroupsupply.com ). It is displayed on the left side under your profile information.
A yellow or green circle implies that you have reached a positive S-Rating. In case of a yellow circle, we recommend that you further improve your SAQ. In case of a red circle, a negative S-Rating was reached by your company site. In this case, please work on the corrective measures indicated that were agreed upon after the On-Site Check as soon as possible and also improve your SAQ.
If the circle is grey, the S-Rating could not yet be determined for your company site. The reason for this could e.g. be that the SAQ score was too low or that an On-Site Check is necessary to determine the S-Rating.
For how long is the S-Rating valid?
The S-Rating is valid up to a maximum of six years. You will be contacted in case measures need to be taken. You can always proactively improve the SAQ score on the NQC platform.
What are the minimum requirements of the Volkswagen Group?
You can find information regarding the minimum requirements here.
When and how can I improve my S-Rating?
The result of your completed SAQ, which forms the basis of the S-Rating, can be edited and improved at any time (except during the validation phase). Improvement recommendations based on your responses in the SAQ can be found on the Supplier Assurance Platform.
Your On-site Check result can generally be improved by implementing the Corrective Action Plan and/or by conducting a re-audit.
If your company receives a score of less than 100 points, you will be issued a Corrective Action Plan (CAP). The measures are documented in the CAP, and their implementation is agreed upon and monitored with the supplier. Depending on the specific measures, you must implement the improvement plan and the described actions within a reasonable timeframe. If the supplier does not address the CAP or fails to do so within the agreed timeframe, or even refuses an On-site Check, they may be excluded from future contract awards (resulting in a "-" or "C" rating). If the supplier receives an audit result of less than 50 points, a follow-up audit will be conducted after the CAP has been implemented.
Which factors influence the S-Rating of my location?
You can find information on influencing factors here.
Who can I contact in case of further questions?
Suppliers can contact the local Volkswagen Group sustainability teams via the following email addresses:
AUDI AG s-rating@audi.de
Bentley s-rating@bentley.co.uk
MAN Truck & Bus cr-purchasing@man.e
Porsche sustainability-procurement@porsche.de
Scania supplier.sustainability@scania.com
SEAT s-rating@seat.es
SKODA s-rating@skoda-auto.cz
Volkswagen AG s-rating@vwgroupsupply.com
Volkswagen de Mexico SiSR-VWM@vw.com.mx
Volkswagen Group China vgc_sustainability@volkswagen.com.cn
Volkswagen Group of America VWGoASustainability@vw.com
Volkswagen Argentina proveedoressustentables@vw.com.ar
Volkswagen do Brasil sustentabilidade2@volkswagen.com.br
FAQs- SAQ
Which suppliers have to complete the SAQ?
In general, the SAQ is relevant for all suppliers. Especially for those, who have a production site and/or supply machinery or tools as well as for suppliers from the areas of catering, cleaning services, logistics, construction, waste management, energy, chemicals, software development, personal protective equipment and scrapping. The request to fill out the SAQ will be sent to our suppliers via email from sustainability@vwgroupsupply.com or by individuals from the Volkswagen Group or its subsidiaries. Suppliers should therefore ensure that the contact information in the Supplier Data Base (LDB) on ONE.KBP is up to date.
The S-Rating is applicable to sites with more than 9 employees. Company sites with 9 employees or less can contact Volkswagen Group to apply for an exception. You can find additional information here.
Please note than the BPDD process is not part of this exception.
How do I complete an SAQ on NQC?
For instructions on how to access NQC and share an SAQ with us, please refer to the introduction video on NQC under the following link:
What can I do if a document has been rejected during the validation?
If certain documents have not been accepted, you will be informed via email. On the platform supplierassurance.com you have the opportunity to see the reasons for rejection by selecting the respective SAQ and clicking the option "View". You will then see a list of the open points and comments.
Reasons for rejection of a document are e.g. insufficient coverage of relevant topics in the guidelines (that were checked as sub-topics) or a lack of documentation of the prevailing management systems. Furthermore, documents often cannot be assigned to the respective companies if the company logo is missing on the documents or if the scope of application does not cover the company site. In order to complete the SAQ , the rejected document needs to be replaced or the answer to the question must be changed to "no" and then re-submitted for validation.
How can I use one SAQ for multiple suppliers?
Suppliers can use a completed SAQ as a template for other locations. You need to create a new location (by clicking on "Start SAQ") and then select "re-use an existing SAQ". After necessary adjustments have been made in the existing SAQ , it can be shared with an OEM and submitted for validation. In case of any problems, NQC’s technical support can be contacted.
How do I receive an invitation code?
You will receive an invitation code via email. This email will be sent to you after completion of the registration process on the Volkswagen ONE.KBP ( www.vwgroupsupply.com ) or in a separate invitation to finalize/improve the SAQ.
How long does it take to validate my SAQ?
It takes up to five business days to validate the SAQ. In this step, NQC checks if the provided documents are valid proof for the information given in the SAQ.
During the validation phase, you cannot make any changes on the SAQ.
Why do I need a policy?
With a policy, you emphasize the meaning of a certain topic for your company and at the same time increase its significance. Furthermore, it provides your employees with guidance for aligning their own actions to the corporate objectives. As a binding frame of reference for external and internal partners, a policy highlights at a glance the values and standards that underpin your company.
How can I delete an SAQ?
On your dashboard on the Supplier Assurance Platform, click on the "Delete" button of the according SAQ displayed under the tab "Location". In order to delete a SAQ, you need to cancel the sharing with the Volkswagen Group.
In case of technical problems, please contact the support of NQC .
What should I do if NQC identifies the DUNS as branch?
First, please register with the DUNS number of your headquarters. As soon as you have registered and are able to log in, you can start a new SAQ and specify the DUNS number of your branch/specific location there.
What should I do if I cannot complete the SAQ because multiple SAQs exist for the same DUNS number?
If you have started several SAQs and entered the same DUNS number in each of them, none of the SAQs can be sent for validation. Please delete the SAQs so there are no more duplicates. As soon as the duplicates have been deleted, you can send your SAQ for validation. If another user has created a SAQ, please contact NQC and ask for access to the existing SAQ.
Why do I need to update my SAQ if it was completed before October 2022?
- The SAQ on the Supplier Assurance Platform has been updated from version 4.0 to 5.0 in December 2022. This update contained changes and additional questions covering legal requirements that affect all Volkswagen Groups’ suppliers .
- Only a SAQ in the version 5.0 can be transformed into a valid S-Rating.
- The update must be made by August 2023 at the latest.
FAQs - On-Site Check
Which service provider have been commissioned to perform On-Site Checks for VOC-Standard on behalf of Volkswagen Group?
The Volkswagen Group collaborates with the following service providers:
Intertek Certifikation GmbH
Elevate Ltd.
Which companies are commissioned to carry out the audit standard: RSCI?
The RSCI audit standard is currently offered by eight audit service providers. Up-to-date information can be found on the following website: Audit Bodies | RSCI .
The company commissioning the On-site Check according to the RSCI standard decides which audit service provider will be used.
What does the On-site Check according to the RSCI standard cost?
In addition to the audit standard used to determine the cost, the size of the company site to be audited (in terms of area and number of employees) and the industry in which the supplier operates are also important factors.
What Is a Corrective Action Plan (CAP) and Why Is It Important?
The so-called Corrective Action Plan (CAP) is a catalog of measures created by the audit company after inspecting the production site. During the closing meeting, all identified deficiencies and how to address them are discussed with you.
The Volkswagen Group conducts audits in its supply chain with the clear objective of improving the sustainability performance of its suppliers through the timely and consistent implementation of the Corrective Action Plan (CAP).
If a supplier receives a score of less than 100 points, they are issued a Corrective Action Plan (CAP). The measures are documented in the CAP, and their implementation is agreed upon and monitored with the supplier. It is especially important that suppliers implement the CAP completely and within the agreed timeframe, as this is crucial for their sustainability rating (S-Rating) and future contract awards. If the supplier fails to implement the CAP or does not do so within the agreed timeframe, or even refuses an On-site Check, they may be excluded from future awards (resulting in a "-" or "C" rating). If the supplier receives an audit result of less than 50 points, a follow-up audit will be conducted after the CAP has been implemented.
Does the On-site Check Replace the SAQ?
It is important to note that the SAQ result and the result of the On-site Check are considered separately. The SAQ must be completed independently of the On-site Check. The On-site Check is conducted independently of the information provided in the SAQ and additionally influences the S-Rating result alongside the SAQ, but does not replace it.
How Do I Receive the Result and the Audit Report?
VOC Standard:
By signing the report, you confirm that you have taken note of it and give your consent for the report to be forwarded to us. The result will then be included in the calculation of your S-Rating.
RSCI Standard:
After successful completion, you can share your result with us via the RSCI platform. A prerequisite for this is an existing trading relationship between your company and Volkswagen AG registered on the platform. By sharing the result, it will be included in the calculation of your S-Rating.
What Should I Do If I Disagree with the Result?
Please raise this directly during the closing meeting with the auditor. If there are discrepancies between the signed Corrective Action Plan and the final report, please contact the audit company and your contact person at Volkswagen AG or the respective Group company.
How Long Is the On-site Check Valid?
VOC standard:
The result of a VOC is valid for 5 years.
RSCI standard:
The result of a RSCI audit is valid for 3 years.
Where Can I Find More Information About the RSCI Standard?
Help and Information on the RSCI Standard:
Further information and support regarding the RSCI audit standard can be found on the RSCI website: RSCI - Responsible Supply Chain Initiative e.V. | VDA via the VDA, and in the Knowledge Hub responsiblebusiness.sharefile.com.
These platforms offer extensive resources and tools to help you successfully complete the audit process and meet the requirements.
Please do not hesitate to contact the RSCI team at rsci@responsiblebusiness.org if you have any questions about the RSCI program.
The RSCI audit standard is primarily aimed at companies with production sites. This target group plays a crucial role in the supply chain and significantly contributes to compliance with sustainability standards.
Benefits of the RSCI Audit:
The RSCI audit offers numerous advantages for your company:
- Time and effort savings: All active members of the RSCI initiative accept audits conducted under this standard. You can share the audit result—similar to the SAQ result—with all members, saving time and effort in demonstrating your sustainability performance to multiple (potential or existing) business partners.
- Improved sustainability performance: Regular audits help identify weaknesses and implement targeted measures to enhance sustainability performance.
- Increased transparency and trust: Compliance with the RSCI standard builds trust with business partners and customers and strengthens your company’s reputation.
Process of an On-site Check
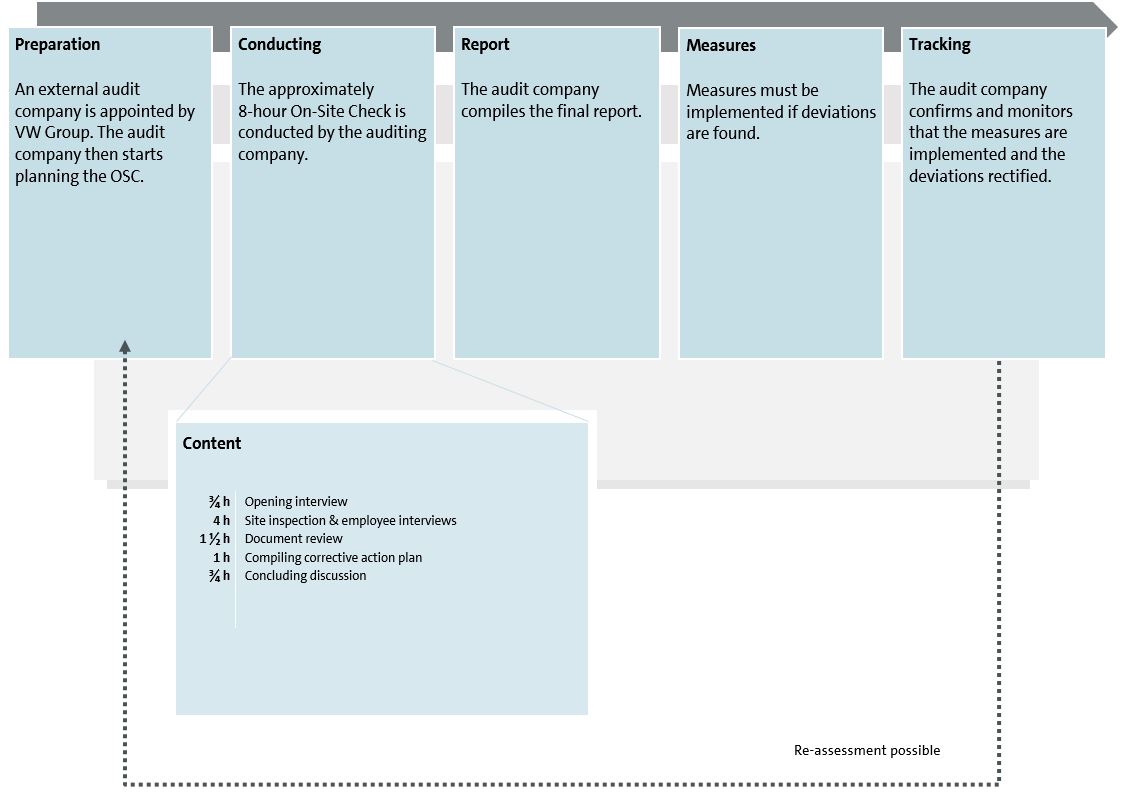
You will receive the request to conduct an On-site Check, along with further information on the next steps, directly via email from the Volkswagen Group.
Depending on the applicable audit standard (based on the type of service provided at the site), either an external audit company will contact you to schedule an On-site Check according to the VOC standard and provide further details about the process,
or you will be asked to independently commission an RSCI audit and share the audit result with us.
Process of an On-site Check According to the VOC Standard
You can find the process illustrated in the following diagram.
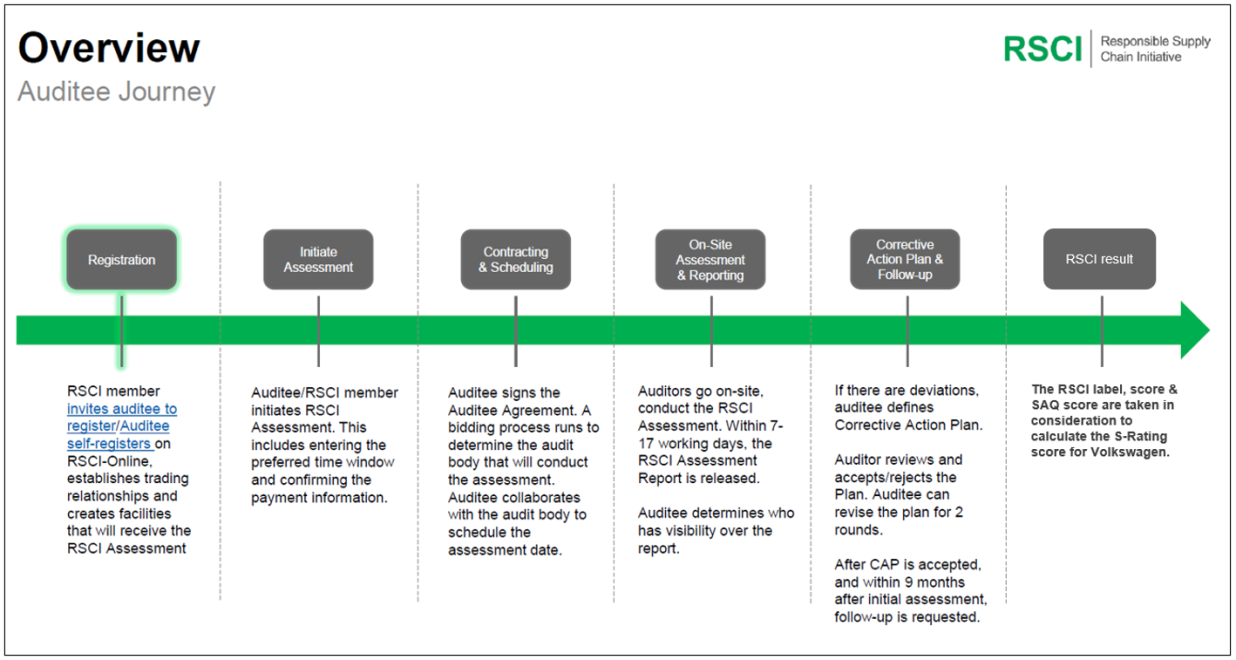
Process of an On-site Check According to the RSCI Standard
You can find the process illustrated in the following diagram.
Here you can find more information:
How Do I Create an Effective Corrective Action Plan (CAP)?
After an RSCI audit, a structured Corrective Action Plan (CAP) is essential to sustainably address identified non-conformities.
Successful CAPs are based on proven methods such as the 5 Whys analysis for root cause identification, the Ishikawa diagram method (Fishbone) for visualizing influencing factors, and the SMART criteria for defining clear, measurable actions.
It is important that each action includes assigned responsibilities, deadlines, and measurable targets. Implementation should be regularly monitored and documented—ideally using a digital action plan. Transparent communication with the Volkswagen Group and the audit service provider, as well as a realistic assessment of implementation timelines, is crucial.
The goal is not just to address symptoms, but to permanently eliminate systemic weaknesses.
What happens after the completion of the CAP and how is the follow-up initiated?
1. Completion of the CAP
- After the initial RSCI audit, deviations are documented.
- The auditee (supplier) prepares a Corrective Action Plan (CAP) to address these deviations.
- The auditor reviews the CAP and approves it if the proposed measures are deemed appropriate.
2. Timeframe for Follow-Up
- A follow-up audit must be conducted within 9 months of the original audit.
- This follow-up serves to verify whether the measures defined in the CAP have actually been implemented.
3. Initiation of the Follow-Up Audit
- Once the CAP is completed and approved, the auditee can initiate the follow-up process via the RSCI platform ("Initiate Follow-Up").
- Before initiating, the Volkswagen Group should be informed.
4. Execution of the Follow-Up Audit
- The auditor revisits the site to verify the implementation of the CAP measures.
- A new report is created to document whether all deviations have been resolved.
5. Issuance of the RSCI Label
- If no critical or fundamental violations remain, the company may receive the RSCI label.
- This label confirms compliance with the social and environmental standards defined by the RSCI guidelines.
Why has my company been selected for a Social Standards Assessment (SSA)?
Your company have been selected for a Sustainability Self-Assessment (SSA), a key element of the Volkswagen Group’s S-Rating. The SSA evaluates compliance with human rights and environmental due diligence, as outlined in our Code of Conduct for Business Partners. Selection is based on a risk assessment considering e.g. product criticality, regional and country-specific risks. The Volkswagen Group regularly reviews its supplier network and contacts the selected suppliers with the support of our Assessment partners.
What topics does the Volkswagen Social Standard Assessment Tool cover?
- General Management: Includes confirmation of valid licenses, permits, transparency, management practices and more.
- Child Labor and Young Workers: Includes verification of no child labor employment, age verification systems, protection of young workers and more.
- Freely Chosen Labor: Ensures facility does not use any forced, bonded, prisoned, or trafficked labor, passports and personal documents are kept by workers, recruitment fees are not charged to workers and more.
- Worker Rights: Validates that there is no verbal, physical, or sexual abuse or harassment, no discrimination, and more.
- Worker Participation: Verifies workers’ rights to bargain collectively and freedom of association are respected and more.
- Working Hours and Payment: Assesses facility practices related to payment of correct wages for regular and overtime hours and adherence to working hour standards and more.
- Health and Safety: Includes evaluation of general work environment, occupational health and safety, and building safety.
- Environment: Reviews facility’s management systems related to environmental standards
- Supply Chain Management: Confirms that management communicates and reviews social and environmental standards to its own business part
What can lead to a red score, and what is needed to meet minimum requirements?
- Scores are determined by both the quantity and the severity of the findings identified. A finding marked with a "zero tolerance" severity rating (such as not providing the required documents or attempting bribery) will lead to a red score directly.
- Red scores may also be a result of several findings identified that are rated critical or major.
- To meet minimum requirements, local laws must be fulfilled.